The EP800 series electric positioner is used in combination with the pneumatic actuator. The input signal of 4~20mA DC is converted into the output air pressure to control the action of the actuator. At the same time according to the formation of the actuator feedback, so that the actuator travel can be positioned according to the control signal. EP800 series electric positioner can be used for single action and double action pneumatic actuators.
2. Features of EP800 series
EPB801 series: Make the basic form for straight - stroke actuators. Single action type is mainly used for thin film actuator, single action type piston actuator, double action type is mainly used for short stroke (100mm) below the double action type piston actuator.
EPB801 series: 5200LA small single action actuator special purpose.
EPB802 series: Used for angular stroke actuator, need special output shaft feedback pin assembly
EPB804 series: Used for angular stroke actuator, actuator output shaft directly feedback, the maximum rotation Angle of feedback rod is 90℃, easy to connect with the actuator directly.
EPB805 series: For straight stroke actuator, feedback lever can rotate 90℃ or 45℃, can be used for longer stroke actuator (410mm below).
EPB808 series: Single and double action direct stroke actuator for pinion and pinion feedback, with special gear box according to the stroke, the stroke is 100~1000mm. When ordering, please follow the required itinerary.
3. Operation principle of EP800 series
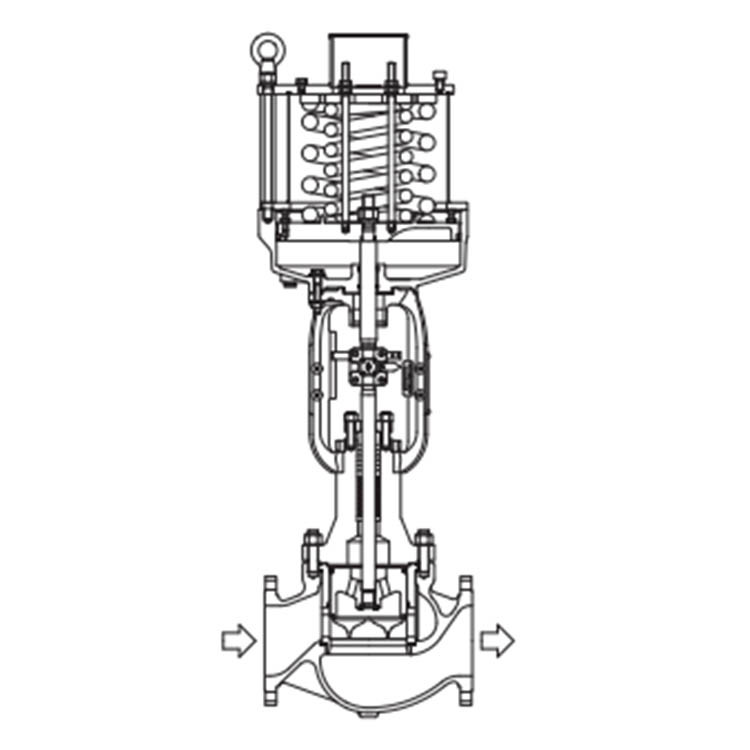
Double action type
Part of the SUP compressed air from the air source enters the back pressure chamber of the nozzle through the fixed throttle and is discharged through the gap between the nozzle and the baffle. After the coil of the torque motor gets the electrical signal I, under the action of the magnetic field, the armature centers on the fulcrum plate spring and turns in the direction shown in Figure A, so that the gap between baffle 4 and nozzle 5 decreases, the back pressure of nozzle increases, and the spool 9 of the control valve moves to the right under the action of air supply pressure chamber 8. Valve 11 of valve hole A10 and valve 12 of valve hole B10 are opened, that is, the compressed air enters the A chamber 12 of the cylinder through the gas pipe OUT1, and the air in the B chamber 14 exhausts outwardly through the gas pipe OUT2. At this time, the piston moves upward due to the pressure difference between the upper and lower cylinder piston. The piston rod rises to drive the feedback rod 17 and the CAM 18, and drives the CAM follower rod 19 and the feedback spring link 20, increasing the tension of the feedback spring 21. The gap between baffle 4 and nozzle 5 is increased. Until the tension of the feedback spring 21 is balanced with the suction force of the input electrical signal I on the armature, the displacement of the piston is proportional to the input signal. In addition, knob 22 can adjust the stroke of the slider 23, knob 24 can adjust the tension of the zero spring 25. And changing the load spring 26 can obtain the corresponding spring characteristic coefficient to adapt to various capacities of the positioner. The above is the rising working state of the piston rod. If the position of the inlet and outlet pipe is changed and the CAM is reversed, the working state is lowered.
Single action type
Part of the compressed air from the air source SUP enters the back pressure chamber 7 of the nozzle through the fixed throttling port 6 and is discharged through the gap between nozzle 5 and baffle 4. After the coil 1 of the torque motor gets an electrical signal I, armature 2 centers on the pivot plate spring 3 under the action of the magnetic field and turns in the direction shown in Figure A to reduce the gap between baffle 4 and nozzle 5 and increase the back pressure of the nozzle accordingly. The control valve spool 9 moves to the right under the action of air supply pressure chamber 8. Valve 11 of valve hole A10 is opened and valve 12 is closed. The pressure in membrane chamber 13 connected with trachea OUT1 rises. Diaphragm 15 gradually rises against the spring 14 force. The push rod 16 rises through the feedback rod 17, and the CAM 18, the CAM follower rod 19 and the feedback spring connecting rod 20, so that the tension of the feedback spring 21 increases, and the gap between the baffle 4 and the nozzle 5 increases. The position of the pushrod 16 is that the diaphragm is in motion until it is in equilibrium with the input signal. In addition, knob 22 can adjust the stroke of the slider 23, knob 24 can adjust the tension of the fog spring 25.
If the A-M manual automatic converter 27 is fully closed, the pressure in the nozzle back pressure chamber 7 rises, the air supply valve 11 is fully open, the air pressure directly through the gas pipe OUT1 into the membrane chamber 13, that is, through the filter pressure reducing valve 28, you can manually operate the action of the actuator. In addition, the replacement of load spring 26 can obtain the corresponding spring characteristic coefficient to adapt to various capacities of positioners. The above is a reaction working state, such as the CAM backloading, can be used for positive action actuator.